In the fast-paced world of industrial operations, efficiency and cost savings are paramount. Enter OPTIFY, our complete portfolio of cutting-edge Industrial Internet of Things (IIoT) solutions, designed to revolutionize how global manufacturers manage their operations. With advanced sensors, breathers, automatic lubricators, gateways, and a robust condition monitoring platform, OPTIFY sets new standards for operational excellence.
In today’s industrial landscape, manufacturers are continually challenged to minimize downtime, reduce maintenance costs, and ensure efficient operations. Traditional methods solely consisting of visual inspection, preventative maintenance, and repairs upon equipment failure fall short—resulting in unplanned downtime, increased expenses, and safety risks. OPTIFY offers a comprehensive solution that directly addresses these critical pain points.
Cost savings and efficiency gains
A leading producer of frozen, ready-to-eat meals adopted OPTIFY to tackle their operational challenges. Running seven production lines around the clock, they needed a robust solution to minimize downtime and enhance productivity. The OPTIFY suite of solutions, from sensors to automatic lubricators and gateways, provided the perfect answer.
The customer integrated OPTIFY across two of their production lines, deploying 106 sensors and 23 Intelli-lube™ drive units. This setup allowed them to monitor and maintain bearings, gearboxes, and motors in real-time to prevent potential failures while minimizing up-front product investment and annual maintenance costs on grease cartridges.
Since implementing sensor technology, the monitored lines have experienced zero unplanned downtime or lost production. The substantial improvements in efficiency have encouraged the customer to expand their use of OPTIFY across all seven production lines.
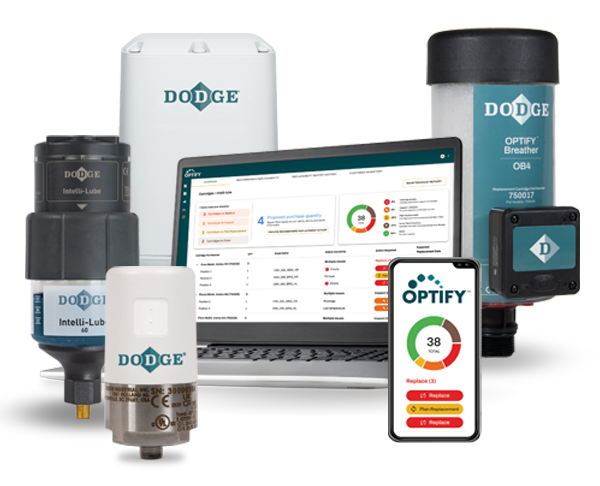
Real-time data and decision-making
One of the OPTIFY platform’s standout features is its ability to provide real-time data, enabling informed decision-making. The customer leveraged this data to optimize their maintenance schedules by pinpointing potential failures and equipment in need of repair prior to failure, allowing them to plan maintenance ahead of time—eliminating unnecessary downtime and improving overall equipment efficiency. This data-driven approach has empowered them to stay ahead of potential issues and maintain seamless operations.
Instrumental to the success of OPTIFY at their facility is the ongoing partnership between plant management and Dodge®. A standing monthly check-in provides ongoing support for any questions that may arise, ensuring smooth implementation and operation.
The plant’s success with OPTIFY has garnered national attention, extending to the corporate chain of command and moving the organization towards the adoption of OPTIFY on a national scale. OPTIFY’s emergence as a standout success for this customer was recently acknowledged when the plant was awarded the “Best Cost Saves/Downtime Avoidance” accolade at their latest Plant Maintenance Manager meeting—highlighting the achievement of the OPTIFY solution and reinforcing their commitment to advance our collaborative efforts.
Ready to get started?
If you are looking to enhance your operations, OPTIFY is the solution you need. Learn how you can revolutionize your plant management with OPTIFY and start your journey towards greater efficiency and cost savings today.